Carbon Steel Welded Tubes
More than 60 years of history has led Marcegaglia to develop the world’s widest range of carbon steel welded tubes in terms of steel grades and dimensions, compliant with the requirements of several industry sectors.
Marcegaglia ERW carbon steel tubing manufacturing is at the core of the group activities since its foundation, and now counts on 150 tube mills worldwide and an overall manufacturing capacity of more than 3 million tons/year. The fabrication process is compliant with all main European norms.
Marcegaglia UK is the largest precision tube manufacturer in Great Britain, with a total output capacity of more than 100,000 tonnes of finished products.
Marcegaglia UK production of carbon steel welded tubes is ISO 9001 certified by SGS since 12/01/1996 and is in according to EN 10305-3, EN 10305-5 and EN 10219 manufacturing standards.
ROUNDED TUBES | |
Min-Max. thickness (mm) | 0.5 – 5 |
Min-Max. diameter (mm) | 12 – 101.6 |
SQUARE TUBES | |
Min-Max. thickness (mm) | 0.70 – 5 |
Min-Max. ext. size (mm) | 12×12 – 80×80 |
RECTANGULAR TUBES | |
Min-Max. thickness (mm) | 0.70 – 5 |
Min-Max. ext. size (mm) | 20×10 – 100×60 |
MANUFACTURING STANDARD - PRODUCT DESIGNATION
EN 10305-3 | Round and shaped precision tubes TREATMENT +CR1 Welded and sized +CR2 Welded and sized |
EN 10305-5 | Square and rectangular precision tubes |
EN 10219 | Cold formed welded structural tubes (CE homologation) |
LENGTHS TOLERANCES
Marcegaglia can guarantee tight tolerances on tube in-line cutting: ±1 mm on standard lengths ranging from 2,000 to 12,500 mm.
OPTIONAL PROCESSING
- Suitability for subsequent galvanizing
- Bead rolling
- Special end finishing
- Cut to length
- Customer defined marking
- Restricted tolerances
- Welding position
- Specific corrosion protection
- Specific packaging method
- Unit testing composed of tubes from a single casting
- Hot galvanization
STANDARD AND OPTIONAL TESTING
- Chemical composition
- Tensile test
- Flattening test
- Expansion test
- Impact test
- Non destructive weld test
- Dimensional test
- Micrographic analysis
- Visual test
- Surface roughness measurement
- Release of special certificates
SUPPLY CONDITIONS
- Dimensional tolerances according to manufacturing standard
- Special tolerances upon request
- Control documents 2.1, 2.2, 3.1, 3.2 according to EN 10204 and specific norm requirements

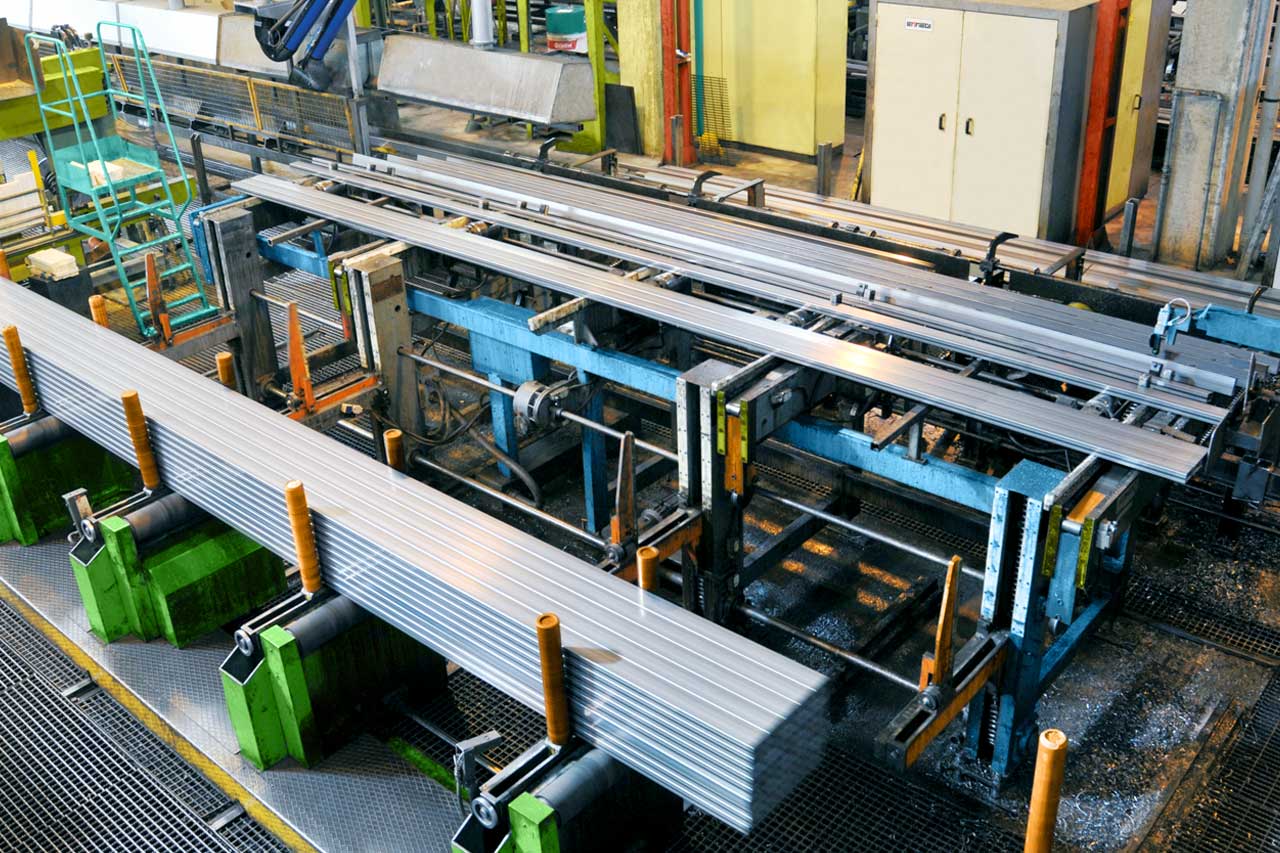
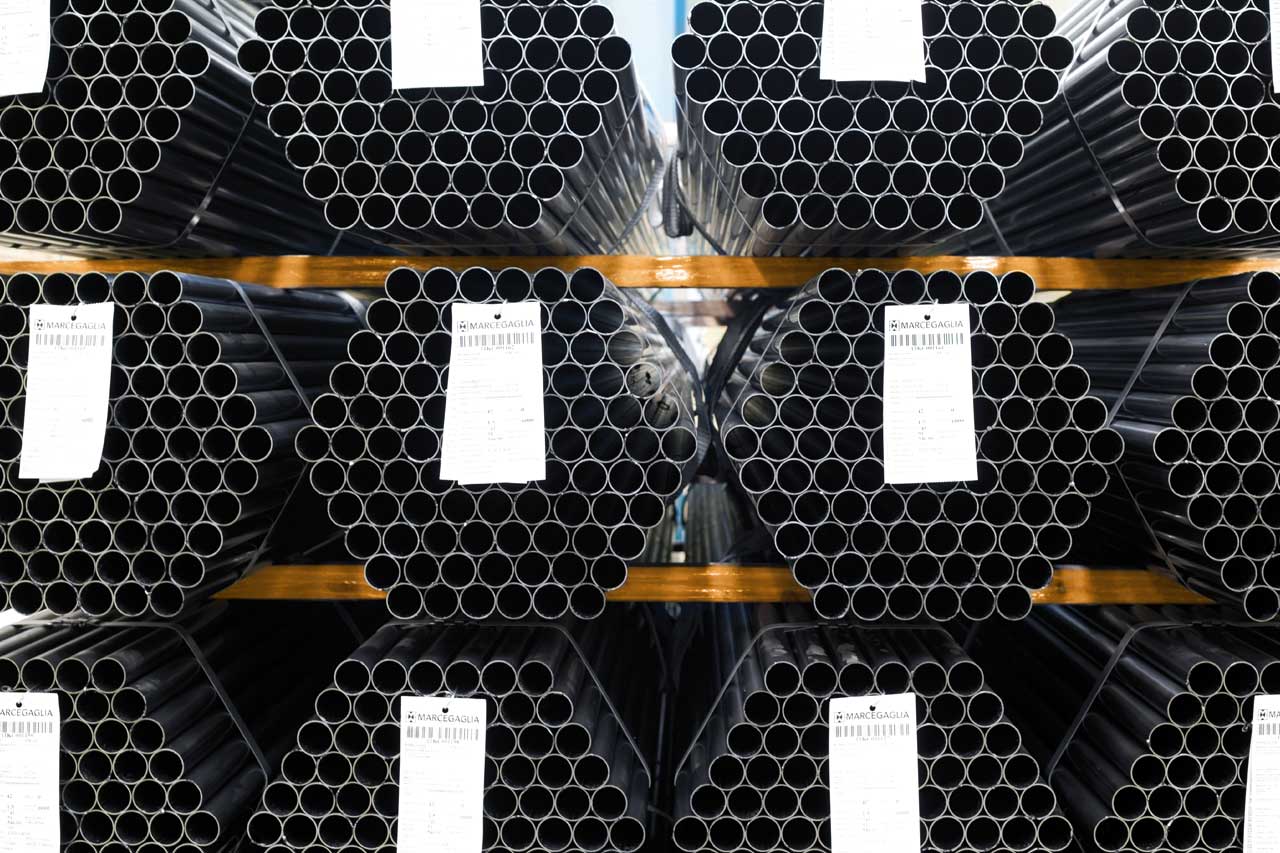

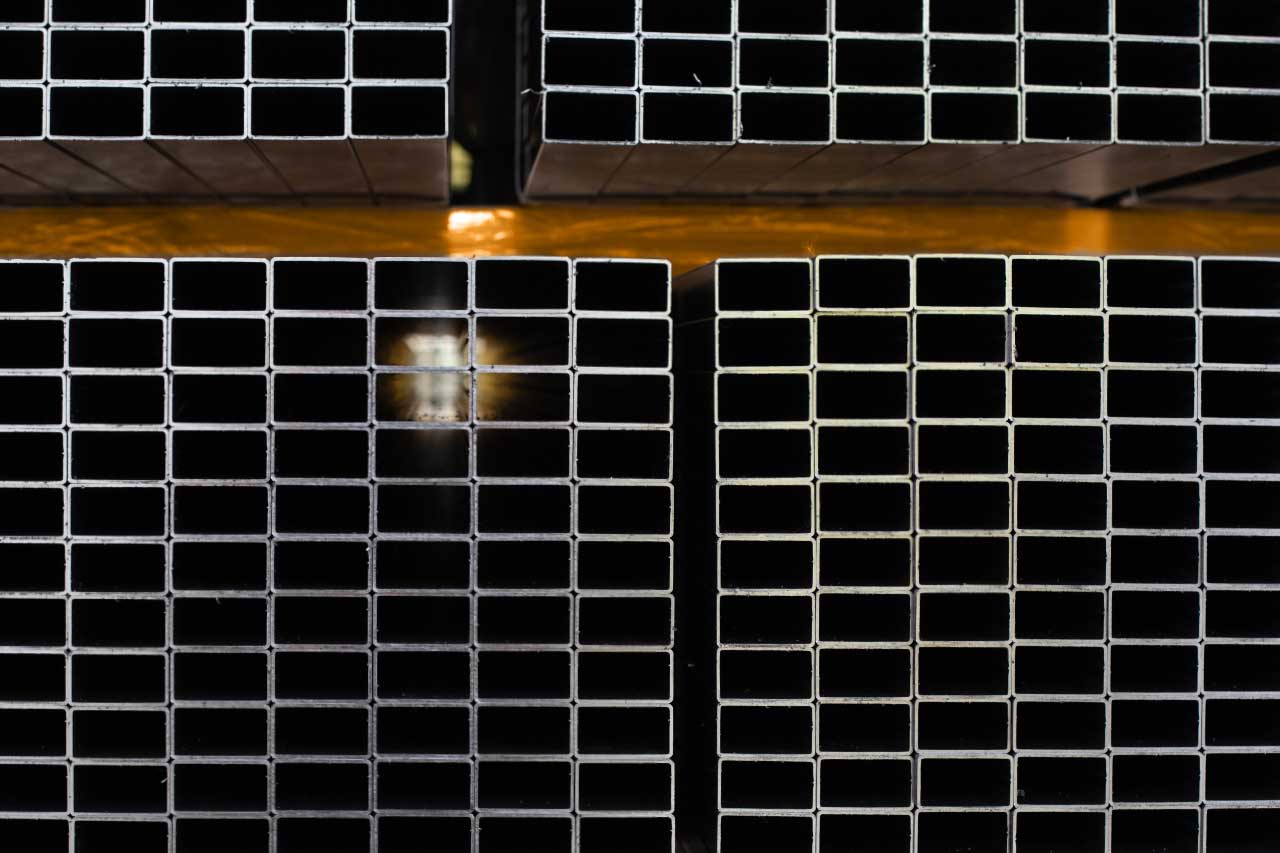
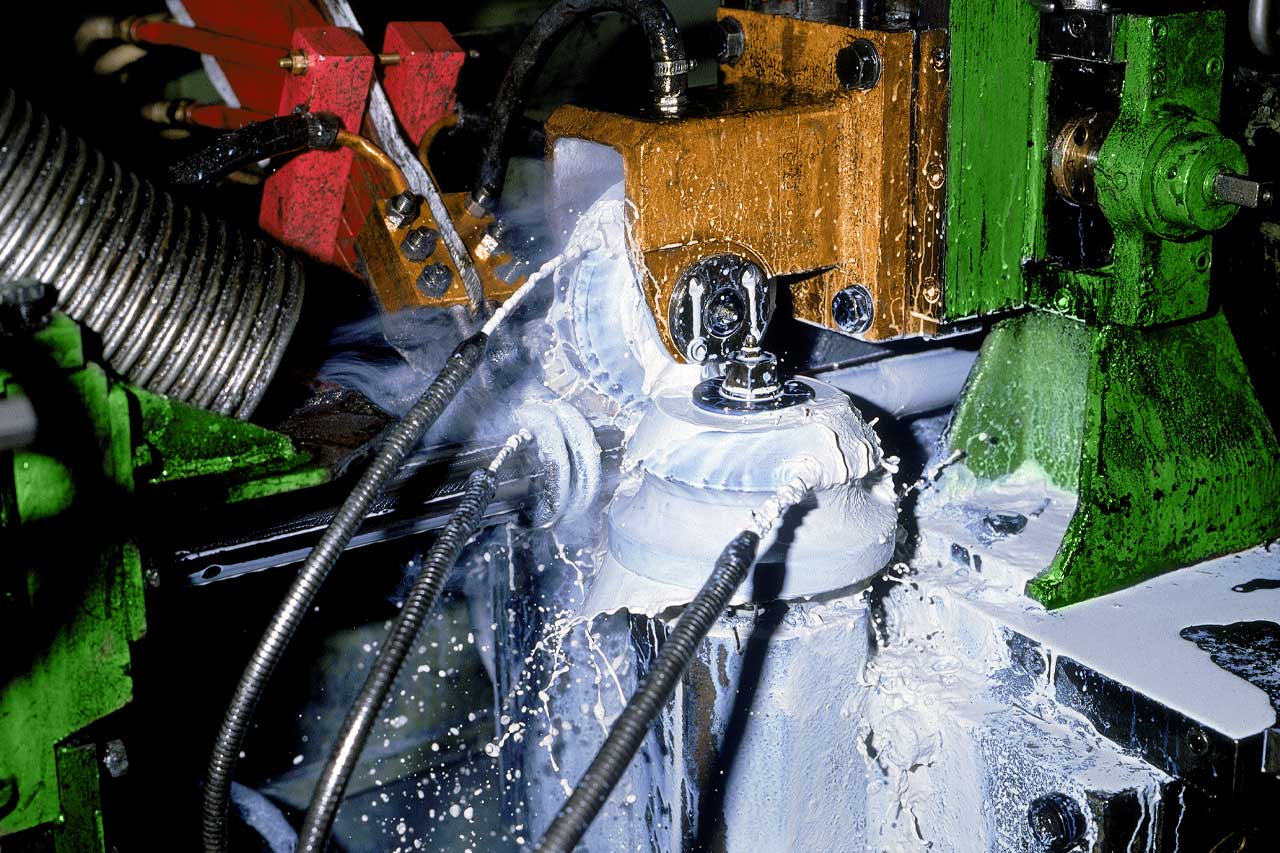
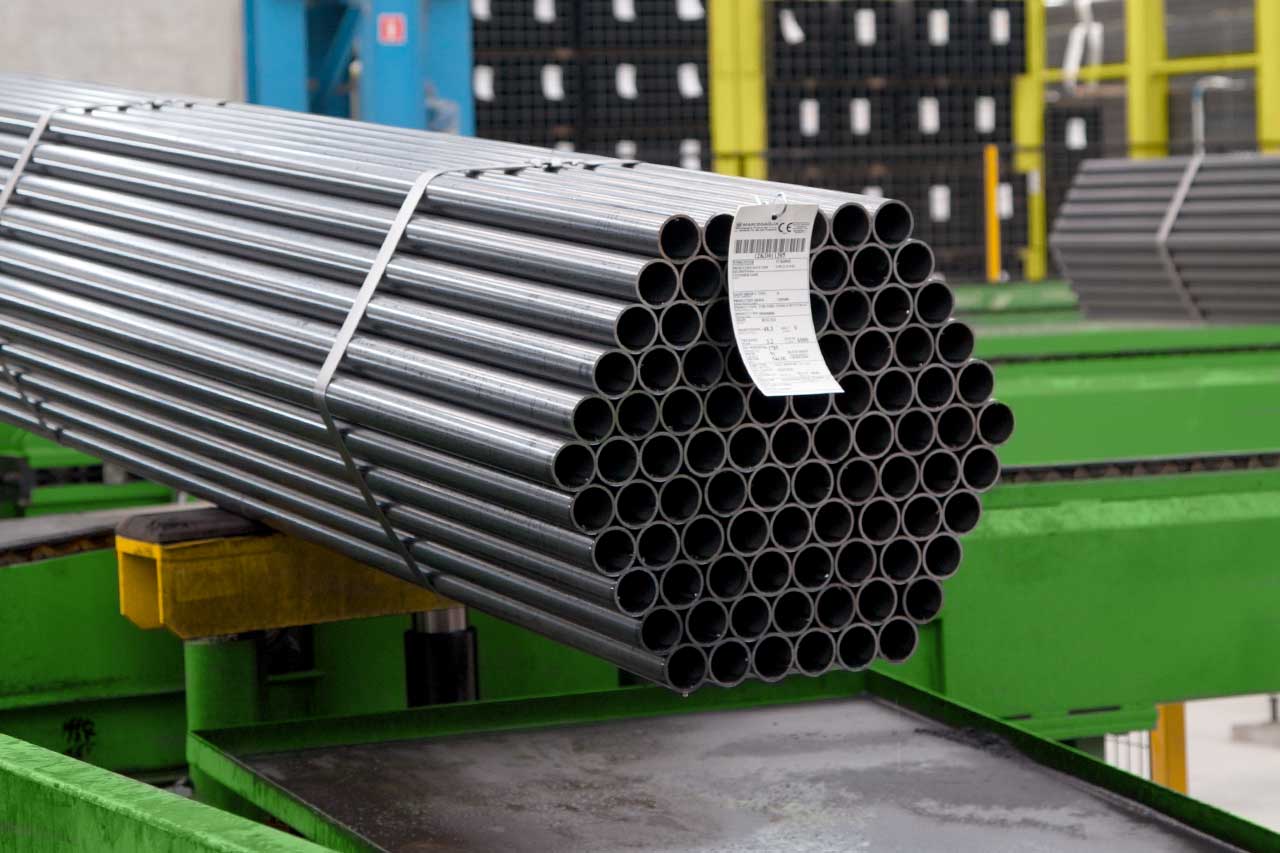
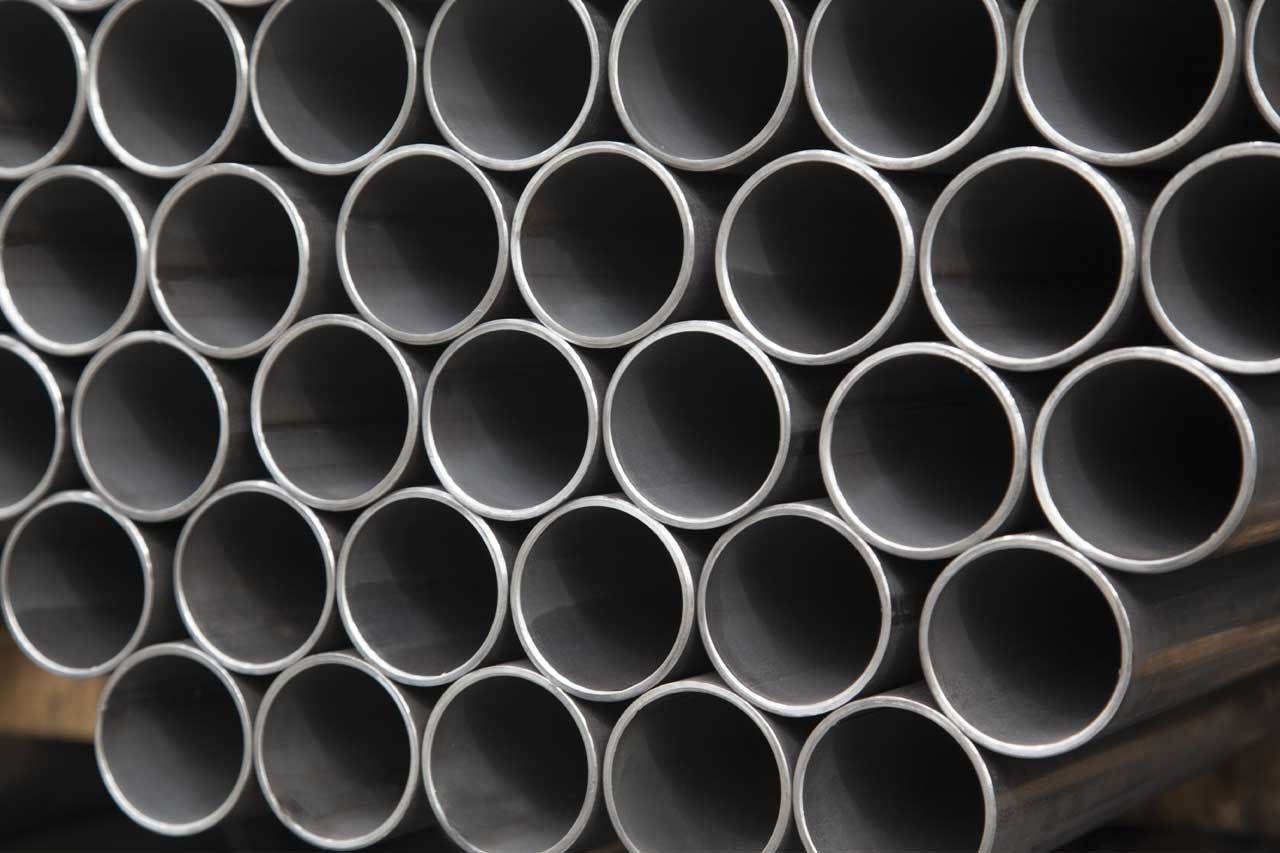